1. Composting.
This is the turning of organic material into humus through, microbial activity. It is completed to avoid scorching plants by directly depositing the organic material which can release some acidic components. To accomplish this, simply compose a pile of the organic matter on a lawn or even in a trench. For fermentation to occur the correct way, which can be aerobic, keep turning the mixture regularly to make sure oxygen supply. Observe the pile until it is fully fermented: loose, odorless with a reliable temperature of 60℃ or 70 ℃. Ensure the water content is 50-60 percent, some straw or sawdust will have the desired effect. Your previously organic waste now turns into organic fertilizer. More detailed info on fertilizer composting process, welcome to https://compostturnermachine.com/composting-process/
2. Deep processing
This is the technique of making the fertilizer above efficient for commercialization through screening, adding nutrients and packaging, all carried out by a processing plant. It is made of two processes depending on the end product you’d want. They are the Powdery organic fertilizer production and Granular organic fertilizer production. The powdery is actually a short process that goes as follows:
Material Crushing:

The fertilizer is crushed into small refined pieces in order to give a smooth mixed powdery product. This is achieved by using a machine called a crusher. The Vertical crusher, particularly, avoids caking, which is solidifying the powder in a cake-like substance.
Screening:
This really is to eliminate any impurities which may be within your powder, ensuring the high quality of organic fertilizer. It is actually done using a rotary screen machine. For the greatest machine, search for the one that is efficient in screening, requires less maintenance, produces low noise and produces small dust amounts.

Packaging:
This is the final step for powdered organic fertilizer. It involves enclosing the finished product in bags for distribution, storage, and sale to customers. The most beneficial machines are automatic packing machines.
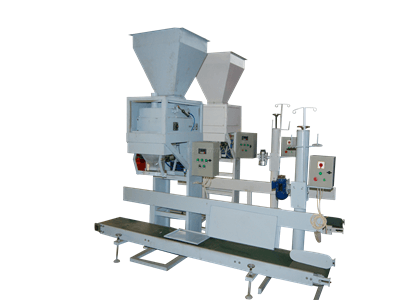
When it comes to Granular organic fertilizer production, the procedure is a little bit more complex and involves a few more steps and machines, therefore. It is going as follows:
Crushing:
This is certainly necessary to produce powdery organic fertilizer and is equivalent to usually the one before.
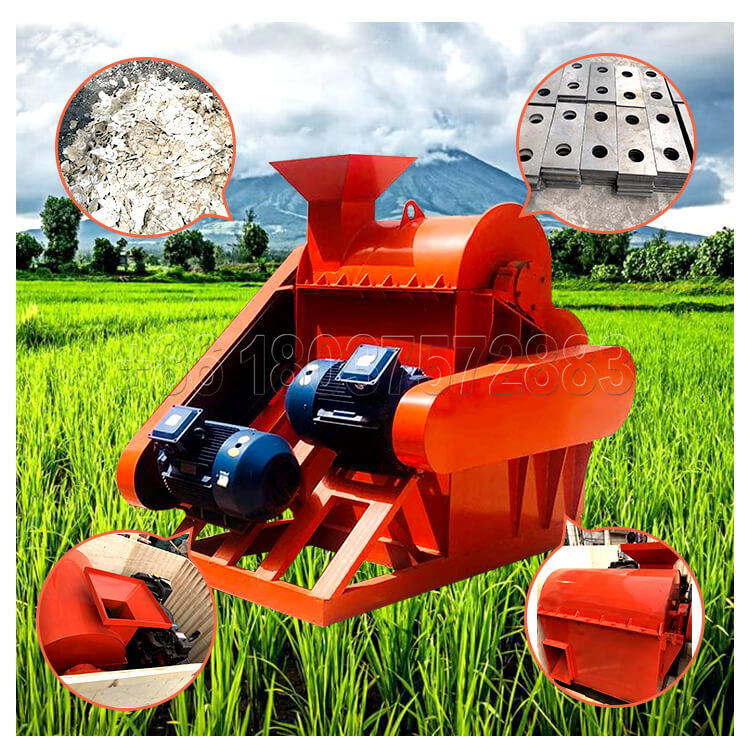
Mixing:
Granular processing demands a highly refined homogenous powder. Additional nutrient elements and functional bacterial can also be added to increase the grade of fertilizer. They may be then mixed together thoroughly by using a disc mixer.
Pelletizing:
This step turns the mixed powder into pellets or granules. Pelletizers can be used for this task. Pellets are simpler to store, manage and package when compared with powder so this is the preferred state of your finished product.
Drying and cooling:
It aims at reducing the water content to improve shelf life.
Screening and packaging.
These adhere to the powder process mentioned there before, only, in such a case, the procedure is on pellets.
In conclusion, the process can provide great value for you personally since everyone seems to be diverging from chemical fertilizers to organic ones. This said it really is a worthy investment.
No comments:
Post a Comment