The fertilizer can be absorbed quickly and efficiently. The nutrients in chemical fertilizer are mainly inorganic and do not need microbial transformation and decomposition. After the application of soil nutrients, they will be absorbed by the roots of crops.
For example, chemical nitrogen fertilizer can be completely released within 3 to 15 days after being applied to the soil, which can quickly meet the needs of crops in the growth stage of plants. Chemical fertilizer can also be applied through irrigation or even leaf coating, which greatly improves the nutrient absorption efficiency of crops.
Fertilizer itself is harmless. Chemical fertilizer has high nutrient content and low impurity. Urea, for example, contains 46% nitrogen. Nitrogen is a nutrient for crops. The rest is mainly Co. When applied to the soil, it is released back into the atmosphere again and is harmless. In addition, it contains about 1% of water and about 1% of urine.
It is strictly controlled below 1.5%. It is harmless to crops and can be decomposed in soil and used by crops and microorganisms. Other phosphate fertilizers, potash fertilizers and trace elements are extracted from minerals, and the basic components are harmless.
Fertilizer machine(https://www.fertilizermachinesale.com/)
Chemical fertilizer improves soil fertility. The nutrient deficiency of common farmland is different. Application of chemical fertilizer can increase crop biomass, increase surface coverage and reduce soil erosion. In addition, the application of chemical fertilizer has increased crop yield, providing a broad space for the development of urban construction, transportation, industry and commerce.
According to the different soil conditions and crop needs, the development of suitable high-efficiency fertilizer products and the scientific and rational application of chemical fertilizer have great potential for agricultural development.
Compost Making Tech, introduces you all the leading compost production technologies, facilities, formulars you want to know
Monday, 29 June 2020
Sunday, 28 June 2020
Belt Conveyor Characteristics
The belt conveyor belt moves according to the principle of friction transmission. Suitable for conveying powder, granular and small materials and bagged materials, such as coal, gravel, sand, cement, fertilizer, grain, etc. The total length and assembly form of the belt conveyor can be determined flexibly according to the user's requirements. The driving device can be an electric roller or a belt driving frame.
Belt conveyor is mainly composed of driving device, driving roller, conveyor belt, idler, tension device, cleaning device, etc.
The driving device transmits the driving force of the motor to the conveyor belt to provide power for the continuous operation of the conveyor belt. It consists of motor, mechanical reducer, coupling and other components.
The driving drum of belt conveyor is a kind of power transmission device. In actual production, it can be divided into single drive drum and double drive drum. It is usually connected and installed by special steel plates by welding. The utility model has the advantages of simple transmission, convenient assembly, convenient disassembly, etc.
The belt of belt conveyor is the part of pulling and conveying materials, so the belt should have enough strength.
The supporting roller of the belt conveyor mainly provides enough supporting force for the belt, and the supporting roller is evenly distributed under the belt to ensure that the belt can run safely and stably when the load is large.
The tension device of the belt conveyor provides enough pre tension for the conveyor belt, so there is a large friction between the conveyor belt and the conveying roller when conveying materials.
The cleaning device of the belt conveyor is mainly used to clean the contents between the conveyor belt, the conveyor drum and the idler, so as to provide a clean and safe operating environment for the conveyor belt.
Belt conveyor can be used for horizontal or inclined conveying. It's very convenient to use. It is widely used in various modern industries, such as mine transportation, mining transportation, fertilizer production line transportation, etc. According to the conveying requirements of the production process, the conveying system can be independent or multi conveyor, or it can be composed of horizontal or inclined conveying system and other conveying equipment to meet the needs of production lines with different layout forms. Click here for more.
Tuesday, 23 June 2020
Organic fertilizer fermentation systems
When organic fertilizer fermentation, organic fertilizer equipment is helpful to prepare organic fertilizer such as chicken, pig, cow dung and straw, which affects the decomposition quality of organic fertilizer and improves the fermentation efficiency of organic fertilizer. The following are the equipment required for the production and fermentation process of organic fertilizers.
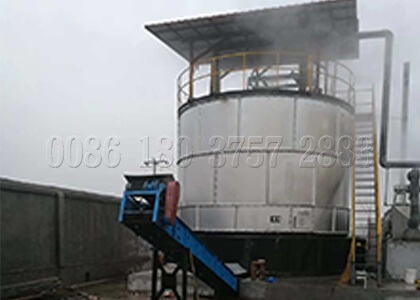
Loader feed hopper
Loader feeding hopper is a new type of machinery that integrates capacity and feeding materials. It is equipped with a storage silo, anti-clump crushing device, out-of-material adjustment system and conveying device. The function can transport the material at a uniform speed and can operate continuously. Especially suitable for large and medium-sized fertilizer plants. For the transfer and accumulation of organic materials during fermentation, it is also suitable for engineering applications such as aquaculture.
Loader feed hoppers are mainly used for mechanized feed and uniform delivery of raw materials. Raw materials can be supplied continuously by forklifts to reduce manual fatigue. There is a crushing and feeding device in the middle of the silo. There is too much material in the silo to start the crushing device. The spindle runs to crush the accumulated material, which makes the material fluffy and remains on the conveyor belt. It is suitable for the uniform transport of various solid materials and certain moisture materials.
Dehydrator
Some fermentation raw materials have too high water content, and dehydration needs to be treated before fermentation.
The machine can be widely used in chickens, cattle, horses, all kinds of animal and poultry manure, wine, starch residue, sauce slag, slaughterhouses and other high concentration for ganic wastewater separation. This machine after the solid liquid separation dehydration, low water content, the appearance of fluffy, no viscosity, no odor, no hand press. After treatment, animal and poultry droppings can be packaged or sold directly. The water content of animal and poultry manure after treatment is the best condition for the fermentation of organic fertilizer of animal and poultry manure, which can be fermented directly to produce organic fertilizer.
1。 The water content is between 80% and 90%, and the water content is between 40% and 50%.
2。 Production capacity varies according to the nature of raw materials: 6-8 cubic meters/hour of chicken manure, 8-10 cubic meters per hour of pig manure, 10-12 cubic meters/hour of cow dung, 10-15 cubic meters/hour of pig manure, 15-20 cubic meters/hour of cow manure.
3。 The main components of the sieve are stainless steel, while the rest are carbon steel.
Straw crusher
In the fermentation raw material, if the straw raw material is too large, it needs to be crushed and processed into small raw materials, in order to shorten the fermentation time of the raw material. Straw shredder can crush corn straw, straw, peanut skin, beans talk, flowers and other burning residue. It avoids the burning of crop straw, protects the environment, and effectively develops renewable energy. The machine is reliable in operation and easy to operate and maintain. The equipment has a wide range of raw materials and is suitable for crop straw.
Organic fertilizer fermentation
Composting dumper
It is a flipmachine for slot compost. Suitable for aerobic fermentation, can be used with solar fermentation tanks, fermentation tanks, transshipment machines. The function of a machine multi-slot can be achieved by matching with the transfer machine. Depending on the width of the groove, the finlimbs can be divided into 3 m, 4 m and 5 m. Different specifications can be customized according to customer requirements and lifting systems can be installed.
Organic waste such as sludge waste, sugar mill filter, inferior slag cakes and straw sawdust are rotated and fermented on this machine. Widely used in organic fertilizer, fertilizer, sludge pile, horticulture pitch, mushroom cultivation plant fermentation compost and dehumidification operations.
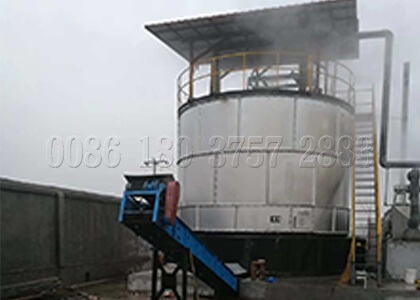
Loader feed hopper
Loader feeding hopper is a new type of machinery that integrates capacity and feeding materials. It is equipped with a storage silo, anti-clump crushing device, out-of-material adjustment system and conveying device. The function can transport the material at a uniform speed and can operate continuously. Especially suitable for large and medium-sized fertilizer plants. For the transfer and accumulation of organic materials during fermentation, it is also suitable for engineering applications such as aquaculture.
Loader feed hoppers are mainly used for mechanized feed and uniform delivery of raw materials. Raw materials can be supplied continuously by forklifts to reduce manual fatigue. There is a crushing and feeding device in the middle of the silo. There is too much material in the silo to start the crushing device. The spindle runs to crush the accumulated material, which makes the material fluffy and remains on the conveyor belt. It is suitable for the uniform transport of various solid materials and certain moisture materials.
Dehydrator
Some fermentation raw materials have too high water content, and dehydration needs to be treated before fermentation.
The machine can be widely used in chickens, cattle, horses, all kinds of animal and poultry manure, wine, starch residue, sauce slag, slaughterhouses and other high concentration for ganic wastewater separation. This machine after the solid liquid separation dehydration, low water content, the appearance of fluffy, no viscosity, no odor, no hand press. After treatment, animal and poultry droppings can be packaged or sold directly. The water content of animal and poultry manure after treatment is the best condition for the fermentation of organic fertilizer of animal and poultry manure, which can be fermented directly to produce organic fertilizer.
1。 The water content is between 80% and 90%, and the water content is between 40% and 50%.
2。 Production capacity varies according to the nature of raw materials: 6-8 cubic meters/hour of chicken manure, 8-10 cubic meters per hour of pig manure, 10-12 cubic meters/hour of cow dung, 10-15 cubic meters/hour of pig manure, 15-20 cubic meters/hour of cow manure.
3。 The main components of the sieve are stainless steel, while the rest are carbon steel.
Straw crusher
In the fermentation raw material, if the straw raw material is too large, it needs to be crushed and processed into small raw materials, in order to shorten the fermentation time of the raw material. Straw shredder can crush corn straw, straw, peanut skin, beans talk, flowers and other burning residue. It avoids the burning of crop straw, protects the environment, and effectively develops renewable energy. The machine is reliable in operation and easy to operate and maintain. The equipment has a wide range of raw materials and is suitable for crop straw.
Organic fertilizer fermentation
Composting dumper
It is a flipmachine for slot compost. Suitable for aerobic fermentation, can be used with solar fermentation tanks, fermentation tanks, transshipment machines. The function of a machine multi-slot can be achieved by matching with the transfer machine. Depending on the width of the groove, the finlimbs can be divided into 3 m, 4 m and 5 m. Different specifications can be customized according to customer requirements and lifting systems can be installed.
Organic waste such as sludge waste, sugar mill filter, inferior slag cakes and straw sawdust are rotated and fermented on this machine. Widely used in organic fertilizer, fertilizer, sludge pile, horticulture pitch, mushroom cultivation plant fermentation compost and dehumidification operations.
Saturday, 20 June 2020
two-in-one granulators features
Advantages of two-in-one organic fertilizer granulators
The new two-in-one organic fertilizer granulator is a combination granulator that can be used for mixing organic fertilizer and inorganic fertilizer. The main way of working is to make the ball by wet method. Fertilizer spun and moved through a certain amount of water or steam in the barrel, creating a squeeze pressure between the material particles to form particles.
The granulator improved the existing problems in the use of the original wet continuous pusher granulation machine, and adopted the rotary cylinder method for the secondary granulation segment and the stirring teeth, which not only met the requirements of particle quality, but also solved the problem of paste wall caused by excessive viscosity and humidity of some materials. It plays an important role in the production line of organic fertilizer and compound fertilizer compound granulation
Raw materials: cow dung, crop straw, wine waste, sage slag, scum, animal waste ,organic fertilizer production line;
Features: high granulation strength, good appearance quality, corrosion resistance, wear resistance, low energy consumption, long service life, adjustable particle size, easy operation and maintenance.
New type of two-in-one organic fertilizer granulation machine
Different types of granulators can select different raw materials. Zhengzhou SX Heavy Industries Technology Co., Ltd. is a professional fertilizer production machinery enterprises in China. We can produce many different types of granulators. Such as double-roller crushing granulator, disc granulator, drum granulator, flat-molded granulation machine and so on. If you are interested in granulators, please visit our website or contact us for more information.
The new two-in-one organic fertilizer granulator is a combination granulator that can be used for mixing organic fertilizer and inorganic fertilizer. The main way of working is to make the ball by wet method. Fertilizer spun and moved through a certain amount of water or steam in the barrel, creating a squeeze pressure between the material particles to form particles.
The granulator improved the existing problems in the use of the original wet continuous pusher granulation machine, and adopted the rotary cylinder method for the secondary granulation segment and the stirring teeth, which not only met the requirements of particle quality, but also solved the problem of paste wall caused by excessive viscosity and humidity of some materials. It plays an important role in the production line of organic fertilizer and compound fertilizer compound granulation
Raw materials: cow dung, crop straw, wine waste, sage slag, scum, animal waste ,organic fertilizer production line;
Features: high granulation strength, good appearance quality, corrosion resistance, wear resistance, low energy consumption, long service life, adjustable particle size, easy operation and maintenance.
New type of two-in-one organic fertilizer granulation machine
Different types of granulators can select different raw materials. Zhengzhou SX Heavy Industries Technology Co., Ltd. is a professional fertilizer production machinery enterprises in China. We can produce many different types of granulators. Such as double-roller crushing granulator, disc granulator, drum granulator, flat-molded granulation machine and so on. If you are interested in granulators, please visit our website or contact us for more information.
Friday, 19 June 2020
Fertilizer conveyor design tech
The bucket lifter is a vertical lifting conveyor. It has the advantages of simple structure, small footprint, low maintenance cost, high conveying efficiency, stable operation and wide application.
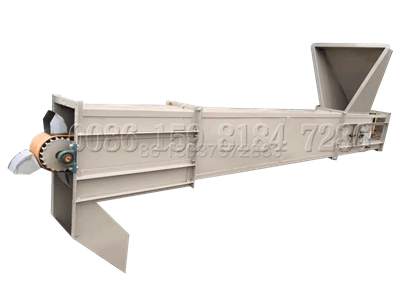
Bucket lifters are widely used in grain, food, feed, mining and other grain and powdermaterial vertical transport. The height of the lift is high, the fertilizer yield is large, and the lifting speed is high.
In fertilizer production, the bucket lifter is an important equipment in the transportation link. The bucket lifter is suitable for conveying powdery, granular, small pieces of material with a mass density of less than 1.5t/m3, such as coal, cement, gravel, sand, fertilizer, grain, etc., and the bucket lifter will extract the material from the following warehouse.
When the conveyor belt or chain rises to the top, it rotates down around the top wheel and the bucket lifter pours the material into the receiving tank.
The belt is usually a rubber band and is mounted on the drive roller and the shift roller. Chain drive bucket lifters are usually equipped with two parallel drive chains, a pair of drive sprockets and a pair of interchange sprockets. Bucket lifters are usually equipped with organic housings to prevent dust from flying in the bucket fertilizer conveyor lift.
In fertilizer production, due to the limitation of workshop area, fertilizer equipment is constructed in vertical space. The bucket lifter plays an important role in material transportation, production process convergence, space utilization and so on.
Wednesday, 17 June 2020
Pig Manure Disposal
Processing technology of organic fertilizer equipment for pig manure
Organic fertilizer production equipment can use organic fertilizer for harmless treatment of pig manure and other animal waste, high organic matter content, reduce the pollution of farm waste discharge to the environment.
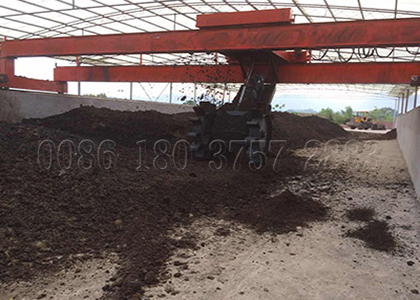
Pig manure organic fertilizer fermentation
The collection of pig manure from the farm, stacked in a fermenter, the collection of attention to the water content of pig manure, generally 40% to 50% is appropriate. Add cotton, wood chips, canola, corn bran and other accessories (prior by straw shredder treatment), the amount of addition is generally 45%-50% of the weight of pig manure, accessories and pig manure fully mixed evenly. During the fermentation of pig manure, microbiological agents are added proportionally and dumped every two or three days. The maximum moisture content in fermentation process is 60%-70%. The temperature of fermentation is low, the intermediate temperature can be up to 60 degrees C, and the temperature is reduced in the later period. Fermentation is 20-30 days in summer and longer in winter.
Organic fertilizer equipment for pig manure
Pre-treatment of organic fertilizer production of pig manure
Fermented pig manure is crushed with a semi-wet material shredder. Use a roller sieve machine to sift out the crushed organic fertilizer powder and prepare processing raw materials. Other nutrients are formulated according to the needs of organic fertilizer and the selected pig manure organic fertilizer is mixed with other nutrients.
Pig manure organic fertilizer granulation processing equipment
Make a compound organic fertilizer into a granular form. There are different types of granulators. According to the needs, the choice of disc granulator, new organic fertilizer granulation machine, roller granulation machine and other granulators, after drying and cooling, can be packaged into commodity organic fertilizer.
Organic fertilizer production equipment can use organic fertilizer for harmless treatment of pig manure and other animal waste, high organic matter content, reduce the pollution of farm waste discharge to the environment.
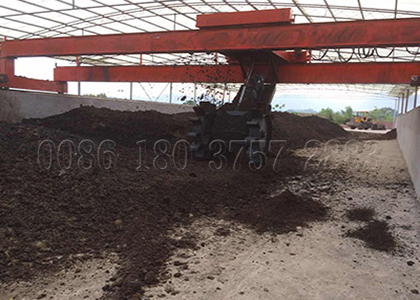
Pig manure organic fertilizer fermentation
The collection of pig manure from the farm, stacked in a fermenter, the collection of attention to the water content of pig manure, generally 40% to 50% is appropriate. Add cotton, wood chips, canola, corn bran and other accessories (prior by straw shredder treatment), the amount of addition is generally 45%-50% of the weight of pig manure, accessories and pig manure fully mixed evenly. During the fermentation of pig manure, microbiological agents are added proportionally and dumped every two or three days. The maximum moisture content in fermentation process is 60%-70%. The temperature of fermentation is low, the intermediate temperature can be up to 60 degrees C, and the temperature is reduced in the later period. Fermentation is 20-30 days in summer and longer in winter.
Organic fertilizer equipment for pig manure
Pre-treatment of organic fertilizer production of pig manure
Fermented pig manure is crushed with a semi-wet material shredder. Use a roller sieve machine to sift out the crushed organic fertilizer powder and prepare processing raw materials. Other nutrients are formulated according to the needs of organic fertilizer and the selected pig manure organic fertilizer is mixed with other nutrients.
Pig manure organic fertilizer granulation processing equipment
Make a compound organic fertilizer into a granular form. There are different types of granulators. According to the needs, the choice of disc granulator, new organic fertilizer granulation machine, roller granulation machine and other granulators, after drying and cooling, can be packaged into commodity organic fertilizer.
Friday, 12 June 2020
NPK fertilizer production
How to avoid fertilizer clumps in NPK fertilizer production
Fertilizer blocking problems usually occur in the process of fertilizer processing, storage and transportation, and are caused by the absorption, dissolution, evaporation and recrystallization of fertilizer particles. In this process, a crystal bridge is formed, causing small particles to form large particles and clump.
So how to avoid the fertilizer clumps generated by NPK fertilization equipment?
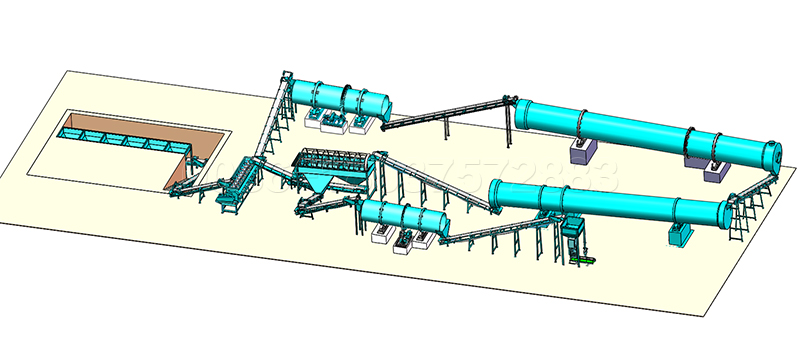
1. Choose the right raw material.
Fertilizer production of raw materials, such as ammonium salts, phosphates, trace element salts, potassium salts, etc., mostly contain crystalline water, easy to absorb water, such as ammonium sulfate, phosphate, trace elements easy to reunite, insoluble in water. Urea is prone to extract water and clumps with trace element salts.
Choose raw materials that are not easy to clump and produce fertilizer that does not clump. For example, fertilizers with humic acid as the main raw material and amino acids as the main raw materials are not easy to clump. Also, try to keep the material dry when selecting it.
2. When producing NPK fertilizer, the water content and packaging temperature of the fertilizer should be reduced and the appropriate production time should be selected.
Fertilizer production is generally non-closed. During the production process, the greater the air humidity, the easier the fertilizer is to absorb moisture clumps. Fertilizer production avoids the rainy season and concentrates on fertilizer production on dry days. In the fertilizer production process, the raw material is heated by dryer, so that the water content of fertilizer is controlled at 0.6%, prolonging the cooling time of fertilizer, reducing the packing temperature, making the fertilizer not easy to clump.
3. Add anti-clumping agent to reduce the physical chemical reaction between NPK fertilizer particles.
The higher the room temperature, the easier it is to dissolve. In general, raw materials dissolve in their own crystalline water and cause clumps. Adding talcum powder, humic acid and other non-clumping powders can also be added some surfactants to prevent clumps.
4. Reduce the height of the fertilizer stacking and storage pressure.
The greater the external pressure of fertilizer, the easier it is for the crystal to clump in contact with the crystal, and the smaller the external pressure, the more difficult it is to clump.
5. The NPK fertilizer can be screened with a screening machine to further improve the uniformity of fertilizer particles.
NPK fertilizer particle size is not uniform, particle spacing is small, contact area is large, easy to reunite. If the pressure strength of fertilizer particles is low, deformation and breakage are easily occurred during packaging, transportation and storage, increasing the contact area between the particles, which can also lead to fertilizer clumps.
If the fertilizer plant uses NPK fertilizer production line to produce a large amount of fertilizer, can be used for two screening machines to obtain suitable fertilizer particles.
6. Production of NPK fertilizer particles.
Because of the small contact area between circular particles, it is not easy to crystallize the clumps. Therefore, the granulation of nitrogen and phosphorus potassium fertilizer is beneficial to the storage, transportation and fertilization of fertilizer.
When using roller granulators to produce NPK compound fertilizer particles, the dryer is not used, but the raw materials for the production of fertilizer must have good adhesion.
When producing NPK compounding particles with a disc granulator (or drum granulator), it must be dried and cooled.
Fertilizer blocking problems usually occur in the process of fertilizer processing, storage and transportation, and are caused by the absorption, dissolution, evaporation and recrystallization of fertilizer particles. In this process, a crystal bridge is formed, causing small particles to form large particles and clump.
So how to avoid the fertilizer clumps generated by NPK fertilization equipment?
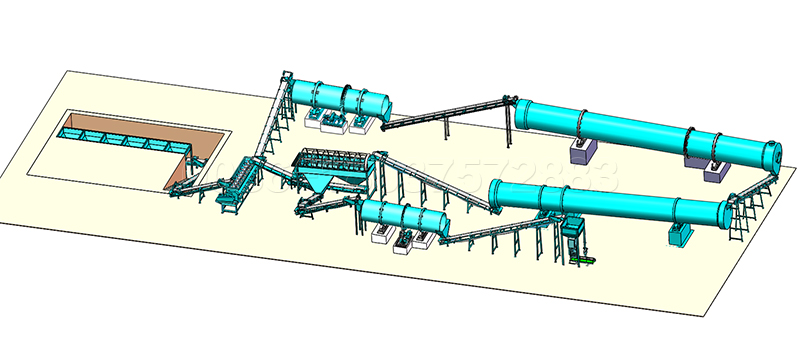
1. Choose the right raw material.
Fertilizer production of raw materials, such as ammonium salts, phosphates, trace element salts, potassium salts, etc., mostly contain crystalline water, easy to absorb water, such as ammonium sulfate, phosphate, trace elements easy to reunite, insoluble in water. Urea is prone to extract water and clumps with trace element salts.
Choose raw materials that are not easy to clump and produce fertilizer that does not clump. For example, fertilizers with humic acid as the main raw material and amino acids as the main raw materials are not easy to clump. Also, try to keep the material dry when selecting it.
2. When producing NPK fertilizer, the water content and packaging temperature of the fertilizer should be reduced and the appropriate production time should be selected.
Fertilizer production is generally non-closed. During the production process, the greater the air humidity, the easier the fertilizer is to absorb moisture clumps. Fertilizer production avoids the rainy season and concentrates on fertilizer production on dry days. In the fertilizer production process, the raw material is heated by dryer, so that the water content of fertilizer is controlled at 0.6%, prolonging the cooling time of fertilizer, reducing the packing temperature, making the fertilizer not easy to clump.
3. Add anti-clumping agent to reduce the physical chemical reaction between NPK fertilizer particles.
The higher the room temperature, the easier it is to dissolve. In general, raw materials dissolve in their own crystalline water and cause clumps. Adding talcum powder, humic acid and other non-clumping powders can also be added some surfactants to prevent clumps.
4. Reduce the height of the fertilizer stacking and storage pressure.
The greater the external pressure of fertilizer, the easier it is for the crystal to clump in contact with the crystal, and the smaller the external pressure, the more difficult it is to clump.
5. The NPK fertilizer can be screened with a screening machine to further improve the uniformity of fertilizer particles.
NPK fertilizer particle size is not uniform, particle spacing is small, contact area is large, easy to reunite. If the pressure strength of fertilizer particles is low, deformation and breakage are easily occurred during packaging, transportation and storage, increasing the contact area between the particles, which can also lead to fertilizer clumps.
If the fertilizer plant uses NPK fertilizer production line to produce a large amount of fertilizer, can be used for two screening machines to obtain suitable fertilizer particles.
6. Production of NPK fertilizer particles.
Because of the small contact area between circular particles, it is not easy to crystallize the clumps. Therefore, the granulation of nitrogen and phosphorus potassium fertilizer is beneficial to the storage, transportation and fertilization of fertilizer.
When using roller granulators to produce NPK compound fertilizer particles, the dryer is not used, but the raw materials for the production of fertilizer must have good adhesion.
When producing NPK compounding particles with a disc granulator (or drum granulator), it must be dried and cooled.
Wednesday, 10 June 2020
Bio-organic fertilizer production process
Bio-organic fertilizer refers to the main raw material of livestock and poultry manure, inoculated with microbial complex bacteria, fermented and decomposed to completely kill pathogens, insects and eggs, fertilizers with microbial fertilizer and organic fertilizer effect, etc. Bio-organic fertilizer generally contains a lot of Nitrogen, phosphorus, potassium and other elements and calcium, magnesium, sulfur, iron, boron and other trace elements, as well as a large amount of organic matter and humic acid substances, make the fertilizer supply balanced. The bio-organic fertilizer production line processes the fermented material into the final organic fertilizer.
Raw material for bio-organic fertilizer production
The main raw materials for bio-organic fertilizer production are agricultural wastes such as livestock and poultry manure and crop straws.
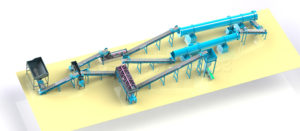
Mixed ingredients in bio-organic fertilizer production
The source of raw materials, fermentation method and equipment are different, and the ingredients are also different. The specific formula depends on the source of the organic material. The general principle of ingredients is: the organic matter content of the total material should be greater than 30% (preferably 50%-70%), carbon to nitrogen ratio (15:1)-(20:1), pH value should be 6-7.5, including The water content should be around 50%, and the water content should be adjusted to 50%-70% during inoculation.
Fermentation maturity
It can be laid flat or fermented in a fermenter. Fermentation tanks are usually placed in closed or semi-closed fermentation chambers. The effect is better than flat ground. Every three days, you need to use a fertilizer turning machine to turn it regularly. After 25-30 days of fermentation, the temperature is gradually reduced from 70-80°C to stable, and the decomposition is completed.
Bio-organic fertilizer production equipment and process
Crushing and mixing pretreatment
Crushing equipment: semi-wet material crusher
This machine is mainly used for crushing biofermented organic fertilizer materials with 25% to 50% moisture. The crushing particle size meets the granulation requirements, and can also be adjusted within a certain range according to user needs. It has a good effect on crushing hard materials such as glass bricks, ceramics and crushed stones in organic fertilizer for municipal solid waste.
Mixing equipment: horizontal mixer
The mixer is mainly used for batch mixing of raw materials, and the materials can be fully stirred. The mixing rate is high and the residue is less. It is suitable for the mixing of feed, concentrated feed and premix additives.
Bio-organic fertilizer production process
Granulation equipment
After composting, the material needs to be granulated to have a certain strength and shape before it can be used as an organic fertilizer. Granulation is a key step in the production of bio-organic fertilizer. There are many types of bio-organic fertilizer granulators. According to the structure of the granulator, the aggregate method can be divided into disc granulator, drum granulator, and new organic fertilizer granulator. According to the position of the press roll, the extrusion method can be divided into a double roll press granulator, a flat die granulator and a ring die granulator.
Disc granulator for bio-granular fertilizer production: Disc granulators are widely used, producing less coarse particles, and the granulation rate is greater than 90%, but the powder fineness requirements are higher.
Drum granulator machine: suitable for mass production of cold and hot granulation and high, medium and low concentration compound fertilizers.
New organic fertilizer granulator: used for granulating organic matter after fermentation, it is the latest technology product with many years of research experience.
Double-roller press granulator: The machine has two shafts, one shaft is fixed and the other shaft is movable. The distance between the two shafts can be adjusted. The shaft material will be extruded between the shafts. The material is granulated at room temperature, no drying process is needed, which saves energy and reduces consumption.
Flat die granulator: There is no need to dry and crush raw materials before granulation. It can directly dispense cylindrical particles and save a lot of energy.
More details of different types of granulators, welcome to https://fertilizergranulatorfactory.com/
Screening equipment
Drum screening machine: There is a certain difference in the particle size output by the granulation molding system, which requires screening and classification. The drum screening machine has the advantages of low vibration, low noise, and convenient screen change. The production line is equipped with an automatic feedback system, which screens the unqualified large and small particles, conveys them through a belt hoist, and then crushes them and sends them to the granulator to continue granulation, which is conducive to improving the continuous operation capacity of the production line.
Vibration screening machine: It has better screening effect on materials, but it has more dust than drum screening machine when working.
Raw material for bio-organic fertilizer production
The main raw materials for bio-organic fertilizer production are agricultural wastes such as livestock and poultry manure and crop straws.
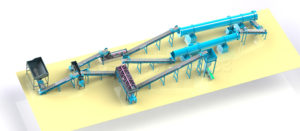
Mixed ingredients in bio-organic fertilizer production
The source of raw materials, fermentation method and equipment are different, and the ingredients are also different. The specific formula depends on the source of the organic material. The general principle of ingredients is: the organic matter content of the total material should be greater than 30% (preferably 50%-70%), carbon to nitrogen ratio (15:1)-(20:1), pH value should be 6-7.5, including The water content should be around 50%, and the water content should be adjusted to 50%-70% during inoculation.
Fermentation maturity
It can be laid flat or fermented in a fermenter. Fermentation tanks are usually placed in closed or semi-closed fermentation chambers. The effect is better than flat ground. Every three days, you need to use a fertilizer turning machine to turn it regularly. After 25-30 days of fermentation, the temperature is gradually reduced from 70-80°C to stable, and the decomposition is completed.
Bio-organic fertilizer production equipment and process
Crushing and mixing pretreatment
Crushing equipment: semi-wet material crusher
This machine is mainly used for crushing biofermented organic fertilizer materials with 25% to 50% moisture. The crushing particle size meets the granulation requirements, and can also be adjusted within a certain range according to user needs. It has a good effect on crushing hard materials such as glass bricks, ceramics and crushed stones in organic fertilizer for municipal solid waste.
Mixing equipment: horizontal mixer
The mixer is mainly used for batch mixing of raw materials, and the materials can be fully stirred. The mixing rate is high and the residue is less. It is suitable for the mixing of feed, concentrated feed and premix additives.
Bio-organic fertilizer production process
Granulation equipment
After composting, the material needs to be granulated to have a certain strength and shape before it can be used as an organic fertilizer. Granulation is a key step in the production of bio-organic fertilizer. There are many types of bio-organic fertilizer granulators. According to the structure of the granulator, the aggregate method can be divided into disc granulator, drum granulator, and new organic fertilizer granulator. According to the position of the press roll, the extrusion method can be divided into a double roll press granulator, a flat die granulator and a ring die granulator.
Disc granulator for bio-granular fertilizer production: Disc granulators are widely used, producing less coarse particles, and the granulation rate is greater than 90%, but the powder fineness requirements are higher.
Drum granulator machine: suitable for mass production of cold and hot granulation and high, medium and low concentration compound fertilizers.
New organic fertilizer granulator: used for granulating organic matter after fermentation, it is the latest technology product with many years of research experience.
Double-roller press granulator: The machine has two shafts, one shaft is fixed and the other shaft is movable. The distance between the two shafts can be adjusted. The shaft material will be extruded between the shafts. The material is granulated at room temperature, no drying process is needed, which saves energy and reduces consumption.
Flat die granulator: There is no need to dry and crush raw materials before granulation. It can directly dispense cylindrical particles and save a lot of energy.
More details of different types of granulators, welcome to https://fertilizergranulatorfactory.com/
Screening equipment
Drum screening machine: There is a certain difference in the particle size output by the granulation molding system, which requires screening and classification. The drum screening machine has the advantages of low vibration, low noise, and convenient screen change. The production line is equipped with an automatic feedback system, which screens the unqualified large and small particles, conveys them through a belt hoist, and then crushes them and sends them to the granulator to continue granulation, which is conducive to improving the continuous operation capacity of the production line.
Vibration screening machine: It has better screening effect on materials, but it has more dust than drum screening machine when working.
Machine Selection Tips
How to choose the right fertilizer turning machine for composting
Fatty fin fish is mainly used for fertilizer fermentation on the farm. The crushed straw and livestock manure need to be fermented to kill a large number of animal feces bacteria, parasites, etc., so as to transform the compost raw materials and shorten the composting time. It is suitable for the mechanism and technological requirements of microbial fermentation of livestock and poultry manure. It can effectively mix fertilizers with microbial preparations and plant straws to create a good aerobic environment for raw material fermentation.
Under this loose material condition, livestock and poultry manure can be heated for 2 days, deodorized for 3 days, and fertilized for about 15 days, effectively preventing the generation of harmful gases such as hydrogen sulfide and amine gas during fermentation, that is, environmental protection and good Bio-organic fertilizer production.
Material pile compost turning machine
The pile turning machine adopts a pile-type ground fermentation process and uses a soft-start steering clutch. The hydraulic push plate does not require manual stacking of raw materials. The use of drum-type hydraulic lifting can greatly save space, time, diesel and manpower, and shorten the fermentation cycle.
It is suitable for small batch production turnover of organic fertilizer, with good economic benefits and low investment.
Simple stacker
It is suitable for aerobic fermentation and can be used in conjunction with solar fermentation chambers, fermentation tanks and mobile machinery. It can be used with mobile machines to realize the function of multiple slots of a machine. The fermentation tank can be discharged continuously or intermittently, with high efficiency, stable operation, firm and durable, and even spreading.
The centralized control of the control cabinet can realize manual or automatic control functions, the electric shovel is durable, the material has a certain number of crushing and mixing functions, and the limit travel switch can play a safety and limit role.
The stacker has high efficiency, stable operation, firmness and durability, and even toss. Widely welcomed by customers, it is the best lathe that our company sells.
How to choose the right fertilizer applicator
Twin-screw compost truck
Feature
. Stirring in raw material conditioning.
. Adjust the temperature of the material stack.
. Improve the permeability of the raw material pile.
. Adjust the water in the raw material pile.
. Realize the special requirements of the composting process.
The screw type compost turning machine is suitable for mass production of organic fertilizer and has economies of scale.
Fatty fin fish is mainly used for fertilizer fermentation on the farm. The crushed straw and livestock manure need to be fermented to kill a large number of animal feces bacteria, parasites, etc., so as to transform the compost raw materials and shorten the composting time. It is suitable for the mechanism and technological requirements of microbial fermentation of livestock and poultry manure. It can effectively mix fertilizers with microbial preparations and plant straws to create a good aerobic environment for raw material fermentation.
Under this loose material condition, livestock and poultry manure can be heated for 2 days, deodorized for 3 days, and fertilized for about 15 days, effectively preventing the generation of harmful gases such as hydrogen sulfide and amine gas during fermentation, that is, environmental protection and good Bio-organic fertilizer production.
Material pile compost turning machine
The pile turning machine adopts a pile-type ground fermentation process and uses a soft-start steering clutch. The hydraulic push plate does not require manual stacking of raw materials. The use of drum-type hydraulic lifting can greatly save space, time, diesel and manpower, and shorten the fermentation cycle.
It is suitable for small batch production turnover of organic fertilizer, with good economic benefits and low investment.
Simple stacker
It is suitable for aerobic fermentation and can be used in conjunction with solar fermentation chambers, fermentation tanks and mobile machinery. It can be used with mobile machines to realize the function of multiple slots of a machine. The fermentation tank can be discharged continuously or intermittently, with high efficiency, stable operation, firm and durable, and even spreading.
The centralized control of the control cabinet can realize manual or automatic control functions, the electric shovel is durable, the material has a certain number of crushing and mixing functions, and the limit travel switch can play a safety and limit role.
The stacker has high efficiency, stable operation, firmness and durability, and even toss. Widely welcomed by customers, it is the best lathe that our company sells.
How to choose the right fertilizer applicator
Twin-screw compost truck
Feature
. Stirring in raw material conditioning.
. Adjust the temperature of the material stack.
. Improve the permeability of the raw material pile.
. Adjust the water in the raw material pile.
. Realize the special requirements of the composting process.
The screw type compost turning machine is suitable for mass production of organic fertilizer and has economies of scale.
Tuesday, 9 June 2020
raw materials of organic fertilizer
Application of organic fertilizer is the key to maintain and improve soil fertility. It is also an important measure to achieve sustainable agricultural development and the recycling of various nutrients. Organic fertilizer plays an important role in balancing crop nutrient supply, improving product quality, and increasing crop yield.
Organic fertilizer raw materials for production
1. Livestock manure
Pig manure, cow manure, horse manure, sheep manure, rabbit manure, poultry manure, silkworm sand, sea bird manure.
Go to SX Livetock Manure Processing for more details.
2. Straw and other plant residues
Straw, straw, corn stover, soybean straw, rape straw, etc. all contain high cellulose and lignin, and are generally used to increase the organic matter of fermentation materials and adjust the C/N ratio. SX CTM introduce detailed steps on plant residue processing into composts, welcome to https://organicfertilizerplants.com/farm-waste-disposal/
3. Cake fertilizer, mushroom residue or furfural residue
Cake fertilizer is the residue of oil extracted from oily seeds, also known as oil cake. It is rich in nutrients, such as bean cake, vegetable cake, peanut cake, tea cake and cypress cake.
Mushroom residue refers to the remaining medium after the edible fungus is harvested, which is mainly composed of the medium and the remaining mycelium.
Furfural residue is the residue discharged from corncob stalks after crushing and adding a certain amount of dilute sulfuric acid under a certain temperature and pressure, after a series of hydrolysis chemical reactions to extract furfural. On mushroom wastes, composting, pls look at how CMSX do, https://compostmachinery.com/mushroom-compost-turner/
4. Sediment in rivers, ponds, ditches and lakes
5. Peat and humic acid
6. Seaweed, etc.
Organic fertilizer raw materials for production
1. Livestock manure
Pig manure, cow manure, horse manure, sheep manure, rabbit manure, poultry manure, silkworm sand, sea bird manure.
Go to SX Livetock Manure Processing for more details.
2. Straw and other plant residues
Straw, straw, corn stover, soybean straw, rape straw, etc. all contain high cellulose and lignin, and are generally used to increase the organic matter of fermentation materials and adjust the C/N ratio. SX CTM introduce detailed steps on plant residue processing into composts, welcome to https://organicfertilizerplants.com/farm-waste-disposal/
Cake fertilizer is the residue of oil extracted from oily seeds, also known as oil cake. It is rich in nutrients, such as bean cake, vegetable cake, peanut cake, tea cake and cypress cake.
Mushroom residue refers to the remaining medium after the edible fungus is harvested, which is mainly composed of the medium and the remaining mycelium.
Furfural residue is the residue discharged from corncob stalks after crushing and adding a certain amount of dilute sulfuric acid under a certain temperature and pressure, after a series of hydrolysis chemical reactions to extract furfural. On mushroom wastes, composting, pls look at how CMSX do, https://compostmachinery.com/mushroom-compost-turner/
5. Peat and humic acid
6. Seaweed, etc.
Monday, 8 June 2020
Chemical Fertilizer VS Organic Fertilizer Granules
Chemical fertilizers, made by chemical or physical methods, contain one or more nutrients needed for the growth of crops. Also called inorganic fertilizer, including nitrogen, phosphorus, potassium, trace elements, compound fertilizer, etc., has the characteristics of strong pertinence and quick results. There are many types of fertilizers, the most common being urea.
Organic fertilizers are formed by various animal and plant residues or metabolites after a certain processing process. It mainly includes agricultural waste, livestock and poultry manure, industrial waste, urban sludge, etc. Organic fertilizer is rich in nutrients and can improve the soil.
Fertilizer pellet machine and organic fertilizer pellet machine
Main fertilizer granulator:
Double roll granulator
The double-roll granulator has the characteristics of compact structure, good stability, good sealing, low noise, easy operation and maintenance, etc. After the new machine is launched, it has won praise from users. It has wide adaptability to raw materials such as chemical fertilizer, feed, chemical industry, especially for rare earth, metallurgy, coal and biological environmental protection. On the other hand, it is also the promotion of environmental engineering.
Disc granulator (disc granulator)
Disc pelletizers are used to make powder into balls, and are widely used in organic fertilizer plants, chemical fertilizer plants, and mining, chemical, and food industries. This machine is used for granulation processing, the appearance of granular products is beautiful, and the size of particle size is large.
Drum granulator
The drum granulator is a fertilizer granulator that can make the material form a specific shape. It is suitable for large-scale production of cold and hot fertilizer granulation production line and high and low concentration compound fertilizer production line.
Main organic fertilizer granulator:
New organic fertilizer granulator
The organic fertilizer granulator is used to granulate various organic substances after fermentation, and is crushed by conventional organic granulation before granulation. The content of organic matter can be as high as 100%, and it is made into pure organic particles, which are spherical.
Ring die granulator
The granulator is used to granulate various organic substances after fermentation, breaking the traditional organic granulation before granulation. There is no need to dry and crush raw materials before granulation. It can directly dispense cylindrical particles and save a lot of energy.
New two-in-one organic fertilizer granulator
The machine can not only granulate a variety of organic matter, especially the crude fiber raw materials that are difficult to granulate with conventional equipment, such as crop straw, wine residue, mushroom residue, medicinal residue, animal feces, etc. It can granulate compound fertilizer. Organic fertilizer and compound fertilizer can be mixed and granulated.
Why organic fertilizer is so popular
Organic fertilizer can improve the damage of the soil, because the organic elements contained in it can restore the vitality of the soil. Excessive use of chemical fertilizers will destroy the soil structure and cause great harm to the soil.
Organic fertilizer improves the plant's resistance to diseases and insect pests, while chemical fertilizer is a single microbial population, prone to diseases and insect pests.
The main equipment of the organic fertilizer production line are: stacker, crusher, screening machine, mixer, granulator, dryer, cooler, screening machine, packaging machine.
Organic fertilizers are formed by various animal and plant residues or metabolites after a certain processing process. It mainly includes agricultural waste, livestock and poultry manure, industrial waste, urban sludge, etc. Organic fertilizer is rich in nutrients and can improve the soil.
Fertilizer pellet machine and organic fertilizer pellet machine
Main fertilizer granulator:
Double roll granulator
The double-roll granulator has the characteristics of compact structure, good stability, good sealing, low noise, easy operation and maintenance, etc. After the new machine is launched, it has won praise from users. It has wide adaptability to raw materials such as chemical fertilizer, feed, chemical industry, especially for rare earth, metallurgy, coal and biological environmental protection. On the other hand, it is also the promotion of environmental engineering.
Disc granulator (disc granulator)
Disc pelletizers are used to make powder into balls, and are widely used in organic fertilizer plants, chemical fertilizer plants, and mining, chemical, and food industries. This machine is used for granulation processing, the appearance of granular products is beautiful, and the size of particle size is large.
Drum granulator
The drum granulator is a fertilizer granulator that can make the material form a specific shape. It is suitable for large-scale production of cold and hot fertilizer granulation production line and high and low concentration compound fertilizer production line.
Main organic fertilizer granulator:
New organic fertilizer granulator
The organic fertilizer granulator is used to granulate various organic substances after fermentation, and is crushed by conventional organic granulation before granulation. The content of organic matter can be as high as 100%, and it is made into pure organic particles, which are spherical.
Ring die granulator
The granulator is used to granulate various organic substances after fermentation, breaking the traditional organic granulation before granulation. There is no need to dry and crush raw materials before granulation. It can directly dispense cylindrical particles and save a lot of energy.
New two-in-one organic fertilizer granulator
The machine can not only granulate a variety of organic matter, especially the crude fiber raw materials that are difficult to granulate with conventional equipment, such as crop straw, wine residue, mushroom residue, medicinal residue, animal feces, etc. It can granulate compound fertilizer. Organic fertilizer and compound fertilizer can be mixed and granulated.
Why organic fertilizer is so popular
Organic fertilizer can improve the damage of the soil, because the organic elements contained in it can restore the vitality of the soil. Excessive use of chemical fertilizers will destroy the soil structure and cause great harm to the soil.
Organic fertilizer improves the plant's resistance to diseases and insect pests, while chemical fertilizer is a single microbial population, prone to diseases and insect pests.
The main equipment of the organic fertilizer production line are: stacker, crusher, screening machine, mixer, granulator, dryer, cooler, screening machine, packaging machine.
Friday, 5 June 2020
Organic Fertilizer Production Procedure
Any smart investor in agriculture knows one thing for certain: Nothing is for waste. With regards to spoiled yield, they can be used green manure, left-overs from harvest bring mulch and in many cases animal waste as manure. They are able to all, however, be also commercialized as fertilizer. Consequently, to make certain success in the industry of creating organic fertilizer within your farm, an operation must be followed for top-quality end product and durability. Listed below are the group of steps to adhere to when you make organic manure:

1. Composting.
This is the turning of organic material into humus through, microbial activity. It is completed to avoid scorching plants by directly depositing the organic material which can release some acidic components. To accomplish this, simply compose a pile of the organic matter on a lawn or even in a trench. For fermentation to occur the correct way, which can be aerobic, keep turning the mixture regularly to make sure oxygen supply. Observe the pile until it is fully fermented: loose, odorless with a reliable temperature of 60℃ or 70 ℃. Ensure the water content is 50-60 percent, some straw or sawdust will have the desired effect. Your previously organic waste now turns into organic fertilizer. More detailed info on fertilizer composting process, welcome to https://compostturnermachine.com/composting-process/
2. Deep processing
This is the technique of making the fertilizer above efficient for commercialization through screening, adding nutrients and packaging, all carried out by a processing plant. It is made of two processes depending on the end product you’d want. They are the Powdery organic fertilizer production and Granular organic fertilizer production. The powdery is actually a short process that goes as follows:
Material Crushing:

The fertilizer is crushed into small refined pieces in order to give a smooth mixed powdery product. This is achieved by using a machine called a crusher. The Vertical crusher, particularly, avoids caking, which is solidifying the powder in a cake-like substance.
Screening:
This really is to eliminate any impurities which may be within your powder, ensuring the high quality of organic fertilizer. It is actually done using a rotary screen machine. For the greatest machine, search for the one that is efficient in screening, requires less maintenance, produces low noise and produces small dust amounts.

Packaging:
This is the final step for powdered organic fertilizer. It involves enclosing the finished product in bags for distribution, storage, and sale to customers. The most beneficial machines are automatic packing machines.
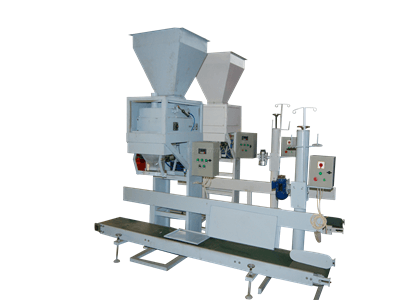
When it comes to Granular organic fertilizer production, the procedure is a little bit more complex and involves a few more steps and machines, therefore. It is going as follows:
Crushing:
This is certainly necessary to produce powdery organic fertilizer and is equivalent to usually the one before.
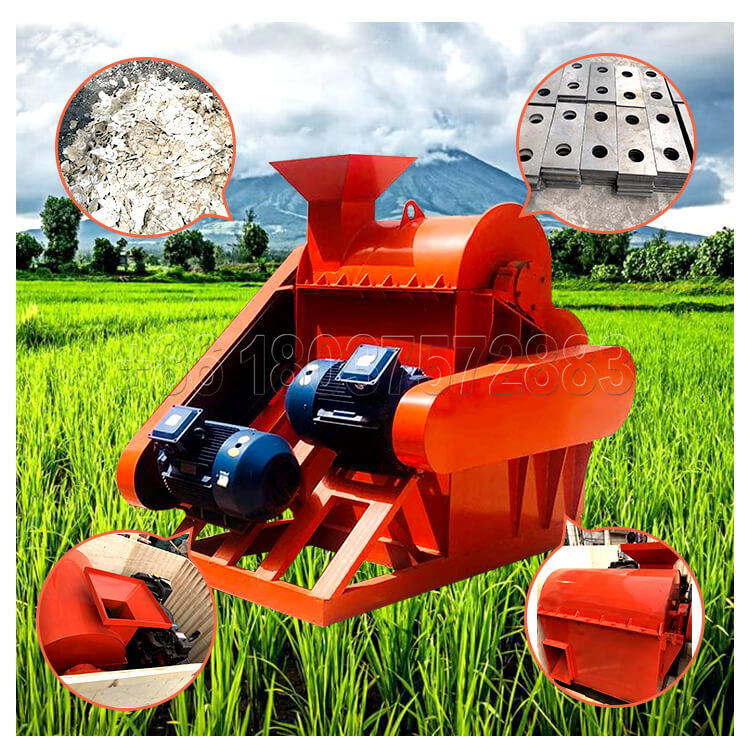
Mixing:
Granular processing demands a highly refined homogenous powder. Additional nutrient elements and functional bacterial can also be added to increase the grade of fertilizer. They may be then mixed together thoroughly by using a disc mixer.
Pelletizing:
This step turns the mixed powder into pellets or granules. Pelletizers can be used for this task. Pellets are simpler to store, manage and package when compared with powder so this is the preferred state of your finished product.
Drying and cooling:
It aims at reducing the water content to improve shelf life.
Screening and packaging.
These adhere to the powder process mentioned there before, only, in such a case, the procedure is on pellets.
In conclusion, the process can provide great value for you personally since everyone seems to be diverging from chemical fertilizers to organic ones. This said it really is a worthy investment.
1. Composting.
This is the turning of organic material into humus through, microbial activity. It is completed to avoid scorching plants by directly depositing the organic material which can release some acidic components. To accomplish this, simply compose a pile of the organic matter on a lawn or even in a trench. For fermentation to occur the correct way, which can be aerobic, keep turning the mixture regularly to make sure oxygen supply. Observe the pile until it is fully fermented: loose, odorless with a reliable temperature of 60℃ or 70 ℃. Ensure the water content is 50-60 percent, some straw or sawdust will have the desired effect. Your previously organic waste now turns into organic fertilizer. More detailed info on fertilizer composting process, welcome to https://compostturnermachine.com/composting-process/
2. Deep processing
This is the technique of making the fertilizer above efficient for commercialization through screening, adding nutrients and packaging, all carried out by a processing plant. It is made of two processes depending on the end product you’d want. They are the Powdery organic fertilizer production and Granular organic fertilizer production. The powdery is actually a short process that goes as follows:
Material Crushing:

The fertilizer is crushed into small refined pieces in order to give a smooth mixed powdery product. This is achieved by using a machine called a crusher. The Vertical crusher, particularly, avoids caking, which is solidifying the powder in a cake-like substance.
Screening:
This really is to eliminate any impurities which may be within your powder, ensuring the high quality of organic fertilizer. It is actually done using a rotary screen machine. For the greatest machine, search for the one that is efficient in screening, requires less maintenance, produces low noise and produces small dust amounts.

Packaging:
This is the final step for powdered organic fertilizer. It involves enclosing the finished product in bags for distribution, storage, and sale to customers. The most beneficial machines are automatic packing machines.
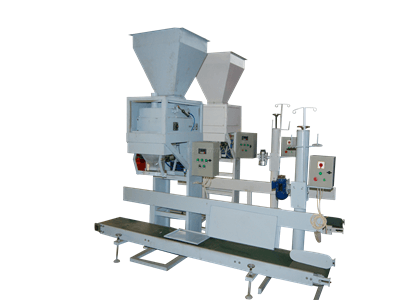
When it comes to Granular organic fertilizer production, the procedure is a little bit more complex and involves a few more steps and machines, therefore. It is going as follows:
Crushing:
This is certainly necessary to produce powdery organic fertilizer and is equivalent to usually the one before.
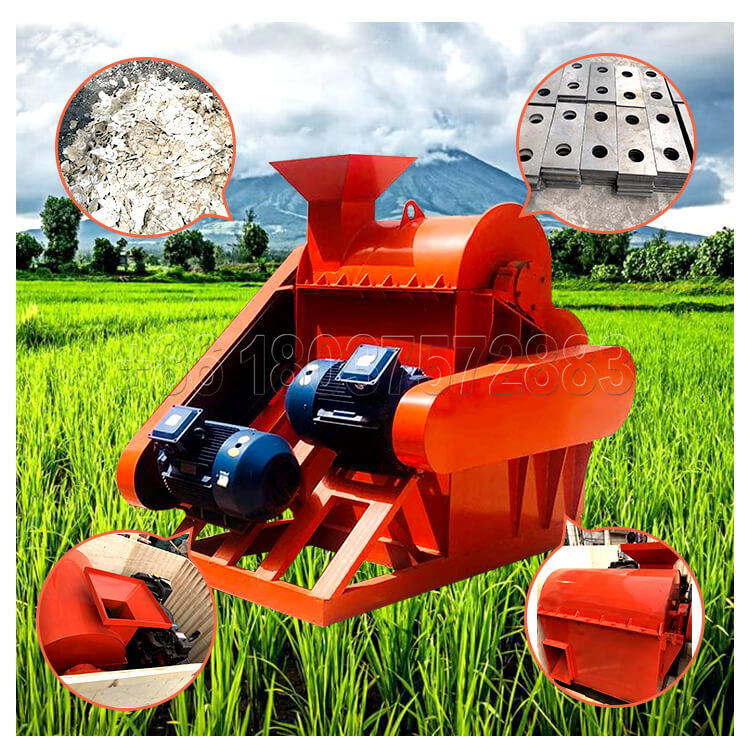
Mixing:
Granular processing demands a highly refined homogenous powder. Additional nutrient elements and functional bacterial can also be added to increase the grade of fertilizer. They may be then mixed together thoroughly by using a disc mixer.
Pelletizing:
This step turns the mixed powder into pellets or granules. Pelletizers can be used for this task. Pellets are simpler to store, manage and package when compared with powder so this is the preferred state of your finished product.
Drying and cooling:
It aims at reducing the water content to improve shelf life.
Screening and packaging.
These adhere to the powder process mentioned there before, only, in such a case, the procedure is on pellets.
In conclusion, the process can provide great value for you personally since everyone seems to be diverging from chemical fertilizers to organic ones. This said it really is a worthy investment.
Thursday, 4 June 2020
Choose Compost Machines Based on Technology
The compost turner machine's primary job is for making organic fertilizer. This procedure happens throughout the fermentation and composting of organic wastes like garbage filters, sludge from industries, mud straw, as well as animal manure, amongst other things. The procedure is inexpensive and in addition ensures zero environmental degradation. The most frequent means of composting is truly the natural way of fermenting by permitting these waste rot away. However, the compost turner machine is very efficient since it adopts these types of technological advancements.
Windrow Composting.
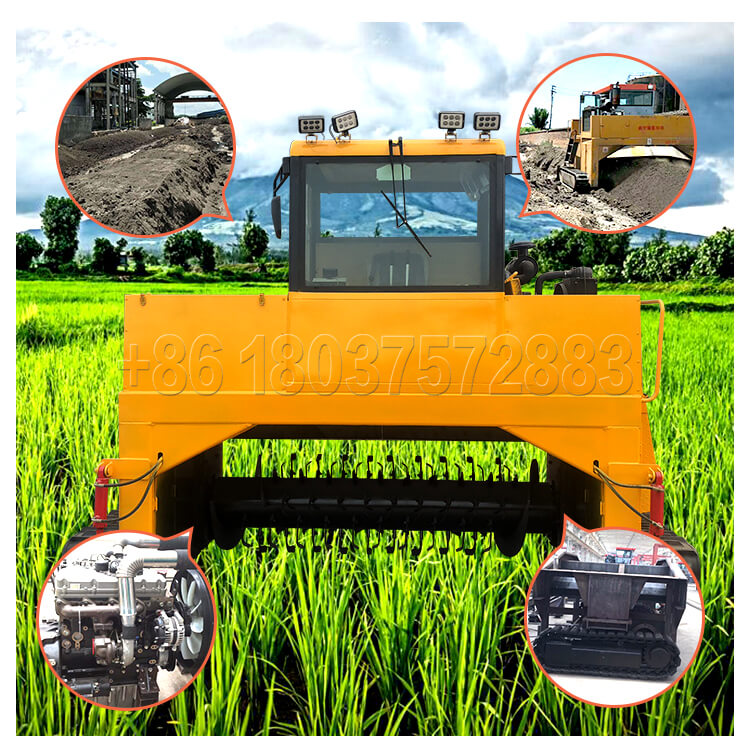
Also referred to as aerated or turned composting. This technology of composting is quite efficient for larger volumes of substances. Almost all of this waste will come from communities hence the extensive collection done by the regional government in a central place. Businesses with good-end food processing activities like restaurants also play a substantial role. This process works by forming organic waste into rows from the name windrows. Later, there exists aeration that can take place at intervals. The ideal windrow height is between four to eight feet, based on the use. Using the size, there exists a guarantee which it will achieve including the flow of oxygen, and enough heat will pass to aid retain the temperatures. Compost Turner taht use windrow composting tech, welcome to https://compostturnermachine.com/compost-windrow-turner/
Vermicomposting

You may always find worms in waste bins, which is their supply of food. However, this feeding helps a whole lot in the creating of compost from your available waste. The waste is split up into high-quality compost through the name castings. Using this technology, worms are actually an excellent business when you quickly purchase them from the market. Therefore, it is very important place this waste in quantities dependant upon the intake of the worms. One pound of worms can eat up to half-pound of organic material. This method takes almost four months to complete. The castings are beneficial since they are available as potting soil. Also, there is certainly another by-product of this technology called worm tea, another type of fertilizer. Here are detailed info and machines related to vermicomposting technology https://manurefertilizermachine.com/industrial-vermicomposting-equipment/
In-Vessel Composting.
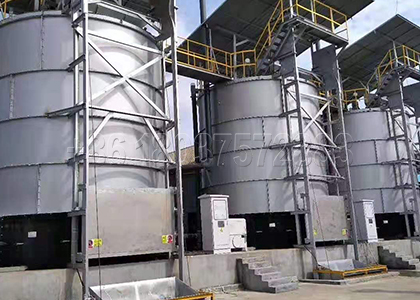
This technology is sufficient as it helps with the composting of organic materials by using minimal space as compared to the windrow method. Also, there is a accommodation of an array of materials from animal manure, food scraps, and biosolids, among other elements. The substances enter into a silo or any other equipment equivalent to a drum. This vacuum ensures there are actually stable airflow and temperature. Mixing from the materials then starts for several minutes to boost aeration. The method takes to a couple of weeks just before the compost is prepared. You use various sizes of drums based on the need of use. More info on in-vessel composting, welcome to https://compostmachinery.com/in-vessel-composting/
Onsite Composting.
Onsite composting can be a composting method efficient for places with minimal levels of organic materials. Organizations producing yard trimmings and average food waste can adapt this method for producing their fertilizers. However, animal merchandise is not recommendable for this sort of composting.
Nevertheless, you can find five essential components of these composting technologies which require strict controlling to ensure the processes are successful. Included in this are sizes of particles, temperature, the flow of oxygen, moisture content, and nutrient balance. Adhering these conditions will yield composts of the finest quality.
Windrow Composting.
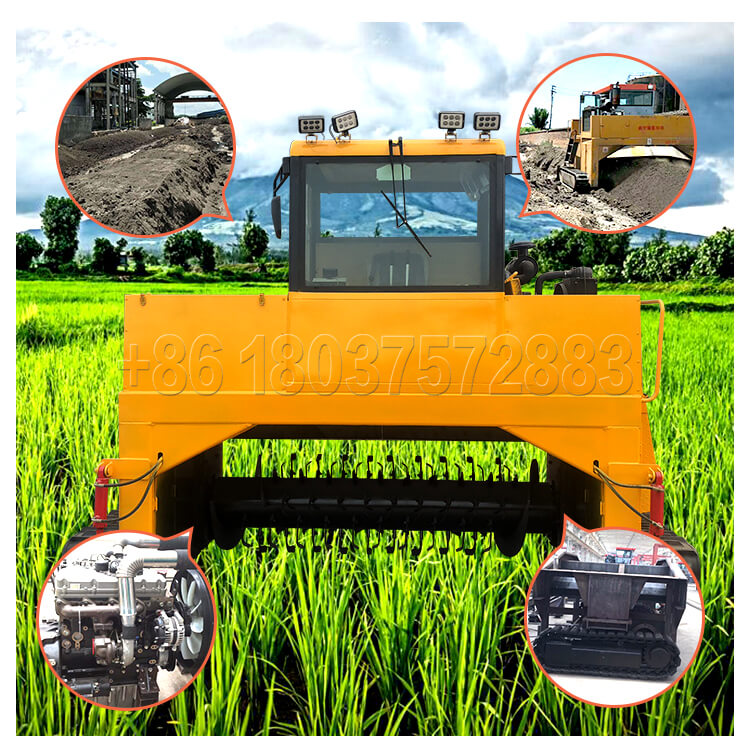
Also referred to as aerated or turned composting. This technology of composting is quite efficient for larger volumes of substances. Almost all of this waste will come from communities hence the extensive collection done by the regional government in a central place. Businesses with good-end food processing activities like restaurants also play a substantial role. This process works by forming organic waste into rows from the name windrows. Later, there exists aeration that can take place at intervals. The ideal windrow height is between four to eight feet, based on the use. Using the size, there exists a guarantee which it will achieve including the flow of oxygen, and enough heat will pass to aid retain the temperatures. Compost Turner taht use windrow composting tech, welcome to https://compostturnermachine.com/compost-windrow-turner/
Vermicomposting
You may always find worms in waste bins, which is their supply of food. However, this feeding helps a whole lot in the creating of compost from your available waste. The waste is split up into high-quality compost through the name castings. Using this technology, worms are actually an excellent business when you quickly purchase them from the market. Therefore, it is very important place this waste in quantities dependant upon the intake of the worms. One pound of worms can eat up to half-pound of organic material. This method takes almost four months to complete. The castings are beneficial since they are available as potting soil. Also, there is certainly another by-product of this technology called worm tea, another type of fertilizer. Here are detailed info and machines related to vermicomposting technology https://manurefertilizermachine.com/industrial-vermicomposting-equipment/
In-Vessel Composting.
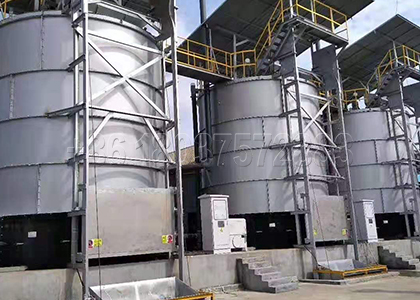
This technology is sufficient as it helps with the composting of organic materials by using minimal space as compared to the windrow method. Also, there is a accommodation of an array of materials from animal manure, food scraps, and biosolids, among other elements. The substances enter into a silo or any other equipment equivalent to a drum. This vacuum ensures there are actually stable airflow and temperature. Mixing from the materials then starts for several minutes to boost aeration. The method takes to a couple of weeks just before the compost is prepared. You use various sizes of drums based on the need of use. More info on in-vessel composting, welcome to https://compostmachinery.com/in-vessel-composting/
Onsite Composting.
Onsite composting can be a composting method efficient for places with minimal levels of organic materials. Organizations producing yard trimmings and average food waste can adapt this method for producing their fertilizers. However, animal merchandise is not recommendable for this sort of composting.
Nevertheless, you can find five essential components of these composting technologies which require strict controlling to ensure the processes are successful. Included in this are sizes of particles, temperature, the flow of oxygen, moisture content, and nutrient balance. Adhering these conditions will yield composts of the finest quality.
Tuesday, 2 June 2020
Guides to Choose Best Compost Making Machine
Compost is absolutely nothing else than recycled organic matter that's very full of nutrients, and therefore an excellent soil conditioner. Even though it costs almost absolutely nothing to make compost, you'll need raw matter along with a special machine. There are many things you may use as raw matter, the most frequent being sawdust pellets, vegetable and fruit scraps, coffee grounds, chicken manure, dead leaves, grass clippings, and also every other type of kitchen and garden waste.
To begin with, you have to determine the amount of matter you want to process every day. Compost machines for commercial and industrial purposes can process from 25 kg per day to 2 tonnes each day. Because this is a significant wide variety, you must narrow it down by determining your actual needs. Always allow some room for growth, if your business develop faster than expected. It wouldn't be too nice to outgrow your equipment in the 1st year of activity. Here are details of compost machines for commercial and industrial purposes https://compostturnermachine.com/commercial-compost-machine/
The productivity rates are another thing to remember when you shop around to find the best machine to make compost. If you want each of the speed you will get, you'd better make an effort to purchase a fully automatic machine. In the event that productivity doesn't matter just as much, you might like to pick a semi-automatic machine instead.
Whatever your decision, ensure that you pick a machine featuring a powerful inbuilt shredder with solid blades, so that you can process even most difficult matter. Check that the power of the motor matches the ability of your shredder. Actually, you'll only want a shredder if you intend to process hard material food waste for example bones. Or else, you save lots of money by selecting a machine without shredder.
An effective machine should in addition have a mixing chamber, power heaters, a gas exhaler and a liquid fertilizer squeezer. The various components of the machine that come into connection with organic matter have to be made from stainless. This can prevent them from rust and may extend the useful lifetime of your machine.
Since composting in not just a mechanical process, you must ask all manufacturers of these equipment for their compost quality certificate. Here is the only method to make sure you're gonna produce high-quality compost.
As a result machines aren't cheap, you shouldn't buy yours from the first supplier you encounter. Always seek for around three quotes from different manufacturers. Moreover, browse the work experience and also the client references of companies on your shortlist. Even though such machines should feature a good warranty, it's usually better to make the buy from an established manufacturer with an effective customer support department.
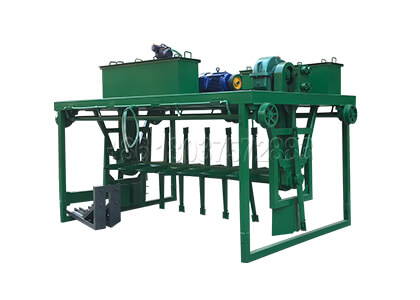
Choosing the right compost making machine depends upon several factors like the raw materials you're going to use, the kind of area you live in, along with your willingness to make the compost manually. In case you desire to make compost to market it to third parties, you'll need a different kind of equipment compared to the average homeowner looking to compost their waste.
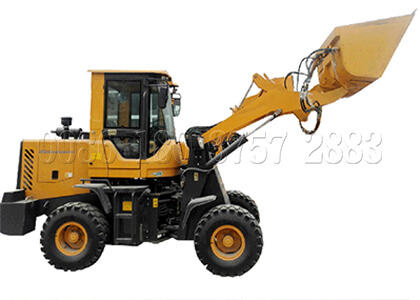
To begin with, you have to determine the amount of matter you want to process every day. Compost machines for commercial and industrial purposes can process from 25 kg per day to 2 tonnes each day. Because this is a significant wide variety, you must narrow it down by determining your actual needs. Always allow some room for growth, if your business develop faster than expected. It wouldn't be too nice to outgrow your equipment in the 1st year of activity. Here are details of compost machines for commercial and industrial purposes https://compostturnermachine.com/commercial-compost-machine/
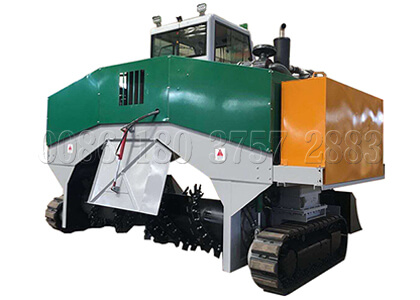
The productivity rates are another thing to remember when you shop around to find the best machine to make compost. If you want each of the speed you will get, you'd better make an effort to purchase a fully automatic machine. In the event that productivity doesn't matter just as much, you might like to pick a semi-automatic machine instead.
Whatever your decision, ensure that you pick a machine featuring a powerful inbuilt shredder with solid blades, so that you can process even most difficult matter. Check that the power of the motor matches the ability of your shredder. Actually, you'll only want a shredder if you intend to process hard material food waste for example bones. Or else, you save lots of money by selecting a machine without shredder.
An effective machine should in addition have a mixing chamber, power heaters, a gas exhaler and a liquid fertilizer squeezer. The various components of the machine that come into connection with organic matter have to be made from stainless. This can prevent them from rust and may extend the useful lifetime of your machine.
Since composting in not just a mechanical process, you must ask all manufacturers of these equipment for their compost quality certificate. Here is the only method to make sure you're gonna produce high-quality compost.
As a result machines aren't cheap, you shouldn't buy yours from the first supplier you encounter. Always seek for around three quotes from different manufacturers. Moreover, browse the work experience and also the client references of companies on your shortlist. Even though such machines should feature a good warranty, it's usually better to make the buy from an established manufacturer with an effective customer support department.
Cow Dung Processing Machine Working Principle
Essential Guide on Costs of Whole Sets of Cow Dung Processing Machines
Provided you can implement cow dung processing machines successfully into the business operations, it is possible to are in position to see fantastic profits. However, many professionals in the market are unaware of the technicalities behind dung processing machinery. If you’re seeking to make the most from these useful machines, you have to take proactive steps to teach yourself in regards to the costs associated with these appliances. With this in mind, here is an important guide about the costs of whole sets of cow dung processing machines.
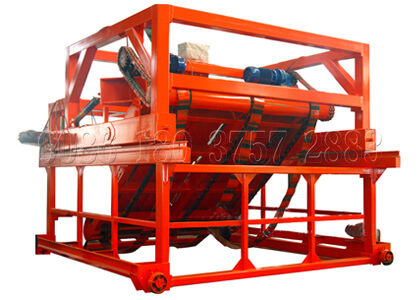
Dependant upon the dung processing machines, you’ll see high variations in operating costs. Certain machines require a lot of power, ultimately causing very high operating costs. Sometimes, the outputs of this equipment is sufficient so that you can justify these expensive fees. However, other times, a machine is merely inefficient and unjustifiably produces high operational costs. You have to develop the capability to examine different models of those machines to evaluate whether or not their associated costs are justifiable, and so, profitable for your company.
There are numerous manufacturers of cow dung processing machines, however, not all of these manufacturers are trustworthy. You should take proactive steps to remove low-quality manufacturers that are infamous in the sector for creating machines that don’t meet standard. These machines could cost high numbers of capital, hence you don’t desire to waste any money on substandard machines. Doing a bit of industry research, you shouldn’t have much difficulty ascertaining which brands are notorious for producing unreliable cow dung machines.
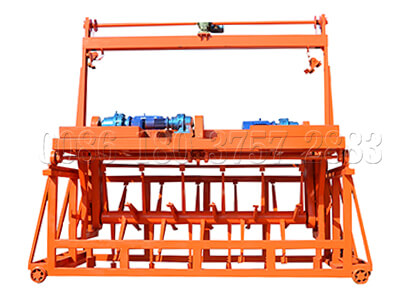
One large cost associated with whole sets of cow dung processing machines is maintenance costs. All machines require maintenance every now and again. Maintenance ensures that the processing machine is not merely working at peak capacity, but additionally makes certain that it won’t malfunction in the near future. Malfunctioning machines can spell financial disaster for just about any business that relies heavily on revenue from dung processing. Make sure that you take into account the varying degrees of maintenance fees related to most of the popular processing machines available on the market currently.
The profitability margins on whole groups of cow dung processing machines are quite high in comparison with other revenue generators in the industry. However, you should always be conservative with regards to financing selections for these appliances. You definitely don’t desire to predicate financing on consistently realizing high margins with these machines. Always look at the worst-case scenario in terms of anything with regards to credit. Hence, always secure the smallest rates possible when financing any acquisition of dung processing machines to deliver both you and your team peace of mind.
The market for cow dung processing machines looks immensely strong in recent times. Now is an excellent a chance to finance some acquisitions of such machines to bolster in the revenue generation potential of the company. However, always make sure that you’re informed concerning the decisions you are making through the entire investment process. Make sure to remember the key points outlined to assure you’ll receive the best processing machines out there.
Provided you can implement cow dung processing machines successfully into the business operations, it is possible to are in position to see fantastic profits. However, many professionals in the market are unaware of the technicalities behind dung processing machinery. If you’re seeking to make the most from these useful machines, you have to take proactive steps to teach yourself in regards to the costs associated with these appliances. With this in mind, here is an important guide about the costs of whole sets of cow dung processing machines.
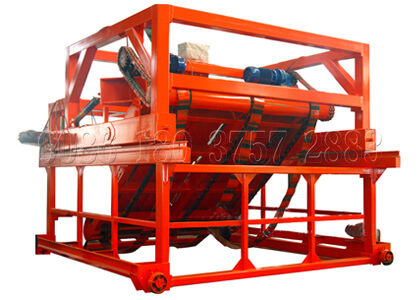
Dependant upon the dung processing machines, you’ll see high variations in operating costs. Certain machines require a lot of power, ultimately causing very high operating costs. Sometimes, the outputs of this equipment is sufficient so that you can justify these expensive fees. However, other times, a machine is merely inefficient and unjustifiably produces high operational costs. You have to develop the capability to examine different models of those machines to evaluate whether or not their associated costs are justifiable, and so, profitable for your company.
There are numerous manufacturers of cow dung processing machines, however, not all of these manufacturers are trustworthy. You should take proactive steps to remove low-quality manufacturers that are infamous in the sector for creating machines that don’t meet standard. These machines could cost high numbers of capital, hence you don’t desire to waste any money on substandard machines. Doing a bit of industry research, you shouldn’t have much difficulty ascertaining which brands are notorious for producing unreliable cow dung machines.
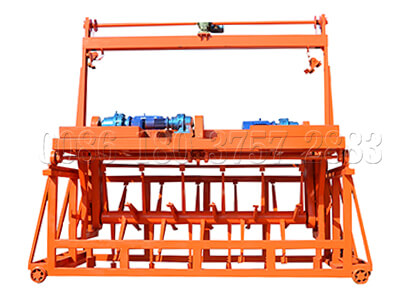
One large cost associated with whole sets of cow dung processing machines is maintenance costs. All machines require maintenance every now and again. Maintenance ensures that the processing machine is not merely working at peak capacity, but additionally makes certain that it won’t malfunction in the near future. Malfunctioning machines can spell financial disaster for just about any business that relies heavily on revenue from dung processing. Make sure that you take into account the varying degrees of maintenance fees related to most of the popular processing machines available on the market currently.
The profitability margins on whole groups of cow dung processing machines are quite high in comparison with other revenue generators in the industry. However, you should always be conservative with regards to financing selections for these appliances. You definitely don’t desire to predicate financing on consistently realizing high margins with these machines. Always look at the worst-case scenario in terms of anything with regards to credit. Hence, always secure the smallest rates possible when financing any acquisition of dung processing machines to deliver both you and your team peace of mind.
The market for cow dung processing machines looks immensely strong in recent times. Now is an excellent a chance to finance some acquisitions of such machines to bolster in the revenue generation potential of the company. However, always make sure that you’re informed concerning the decisions you are making through the entire investment process. Make sure to remember the key points outlined to assure you’ll receive the best processing machines out there.
Subscribe to:
Posts (Atom)